Newsroom Renova
News & Videos
Revolution featured on IPBI – March 23
Continuous line speed changes, slowdowns during splicing, paper tearing, slippage and paper waste… a few of the many issues that often occur during the corrugating process. Customers report excessive downtimes, but even knowing the cause, there aren’t real solutions yet, negatively affecting the corrugating process efficiency.

Furthermore, recent events have caused disruptions to the global energy market and putting businesses worldwide under enormous pressure, leading them to production cuts and price increases as demand declines. The abilities to control energy costs and ensure energy independence are crucial today to address the rapid changes that all companies are experiencing.
For these main reasons, Renova has devised and patented a system with the aim of improving every phase of the production line: Revolution, energy-recovery hybrid brake.
Revolution’s patented design is the combination of a regenerative motor and a pneumatic brake, which operate with “hybrid regulation”: brake and motor always work in tandem ensuring maximum performance in all working conditions.
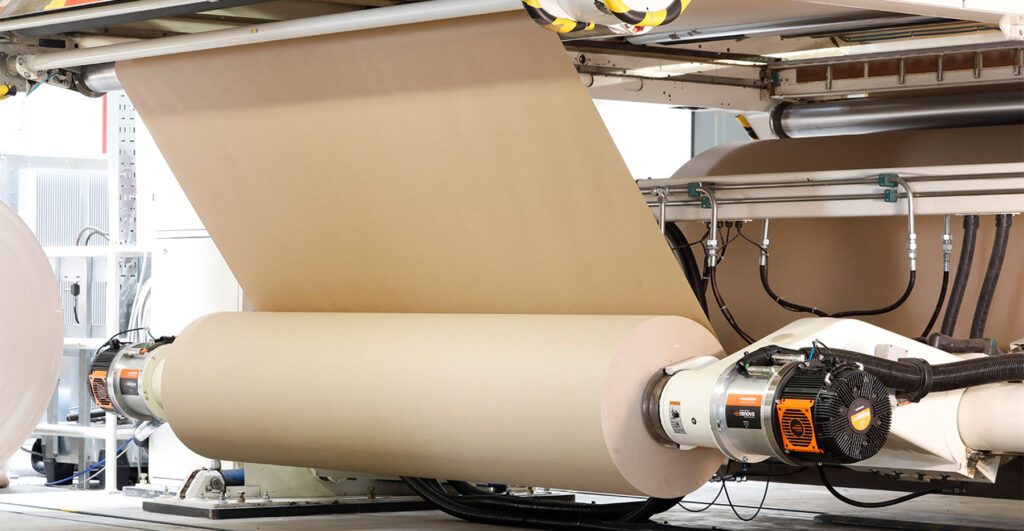
After a close cooperation with our customers, we noticed that they suffered from frequent downtimes during splicing caused by paper tearing, adversely affecting production. In fact, during this phase, the web is pulled via the splicing tape by the draw while the roll, which can reach 5 tons, is still stationary. For this reason, breakages occurred mainly due to low-weight papers or because the tape did not grip correctly.
To avoid paper tearing, the line speed is drastically reduced during splicing, leading to a massive reduction of linear meters produced during each shift.
On the contrary, Revolution accelerates the roll on its axis, and not via paper web, helping the roll in overcoming initial inertia, for an intense reduction of downtimes. This way it’s also possible to keep faster splicing speeds, increasing production.
All corrugators employ pneumatic brakes that emit thermal energy, usually dispersed in the environment. The heat, in addition, accelerates components wear and affects braking efficiency.
Revolution system partially recovers this unexploited energy: the motor transforms the thermal energy of the brake, otherwise lost as heat, in 2kWh per roll stand of electrical energy, that can be reused in the plant’s electrical line.
Furthermore, thanks to the hybrid regulation the brake works less, for a reduced consumption of the pads. This improves paper quality and avoiding waste, a fundamental goal for safeguarding the plant’s economy as well as for the planet’s ecology.
The Renova Revolution allows every corrugator the opportunity to splice at line speeds at least 25% faster and also take advantage of green energy tax credits to make sure they’re making more money without needing more labor.
Revolution is 100% plug&play. An easy and fast installation is always ensured, as it is equipped with customizable flange that allows to retrofit all roll stands with different shaft or chuck configurations.
Revolution is an Industry4.0 technology: the integrated system also includes an intuitive and easy to use control panel that enables to establish a direct dialog with the production systems in the ERP; and a cabinet which contains all the electronic components, connecting Revolution with the plant electric line.
What are you waiting for? The Revolution is here!